The COVID-19 crisis continues to play out at breakneck speed, challenging business models, global supply chains and leading to huge losses on a professional and personal basis.
For manufacturers, it's been a mixed bag.
In the early days of the pandemic, the admirable reaction from many factories was to assist in supplying critical equipment such as personal protective equipment (PPE) and ventilators, if they were able.
Now, in hot verticals such as food supply, logistics, alcohol or hygiene products – assuming the region or country is not in total lockdown – the need to react, adjust, improve flexibility, and carry-on manufacturing operations remains the challenge.
The longer-term implications of the pandemic are already suggesting a rebalancing of offshoring strategies that have dominated global supply chains for the past 30-40 years. Driven by necessity, political will, law and incentives, we could witness a surge in manufacturing investment back to countries that have let the industry dwindle.
Now, more than ever, it is crucial to future-proof your manufacturing operations, and through smart decision-making and adopting a digital-first, cloud-based operation – it is possible.
Embrace a digital-first philosophy
In Australia and around the world, the manufacturing industry is moving toward a new enabling model.
Thanks to restrictions and other limiting factors related to the pandemic, the enabling model involves relocating non-critical operational staff, management and administration to the home office - leaving operators, supervisors and essential maintenance workers to continue the manufacturing and distribution processes on site.
With ever-changing living and workplace conditions globally - restrictions or otherwise - this model may persist for some time, thus accelerating the adoption of virtual technologies that allow site monitoring from afar.
In early 2020, we polled many customers to ascertain how they were maintaining a semblance of normality when it came to production management and organisational control. The replies ranged from “we are struggling” to “we are coping well”.
The companies thriving had systems, processes and automation to ensure communication flowed to all stakeholders effectively. They adopted a digital-first philosophy - implementing scalable, mobile-enabled systems - providing similar visibility of site activities whether on the factory floor or at home with an iPad.
This is now becoming mandatory.
Manufacturing from home
One such company embracing a digital-first philosophy to ensure smooth manufacturing operations amid the COVID-19 pandemic is Adelaide-based company, Oliveri.
Here, the operations management team access real-time data on equipment status, production targets, workforce activities, stoppage reasons and maintenance issues, allowing them to respond to problems immediately.
John Woodcock‘s home office with TilliT including Scheduling, Execution, ERP and all the essentials to remotely monitor the manufacturing operations in Regency Park, South Australia.
John Woodcock, General Manager at Oliveri, can monitor sales, supply chain, production schedules and execution from his home office. Establishing an operations control centre at home, John doesn't have to constantly call various managers to assess the status of the business. This allows him to focus on what matters, coordinating the entire supply chain from raw material to customer satisfaction across a geographically diverse market.
Oliveri chose a suite of web-based tools instead of traditional onsite execution systems. Through secure access, John’s production schedulers, operations supervisors and management can create, publish, update plans, monitor order status, orchestrate all manufacturing processes and communicate with clients at all times.
"Technologies such as these have reduced my requirement to constantly speak to my team on the phone. We are operating as normal, only managing deviation and issues by exception."
Oliveri GM, John Woodcock during a status call in early 2020.
Being present on the shop floor remains ideal. However, with the ongoing unknowns surrounding restrictions Australia-wide, these tools have allowed them to maintain supply, avoid disruption and pivot quickly to the new normal of partial remote operations.
Without IoT and cloud software technologies, this would be a lot more difficult.
Be future-ready in the cloud
Most manufacturing execution and enterprise processes can now effectively reside in the cloud.
Only critical, real-time control systems that manage machinery and equipment processes are required on-premise – and access to these can also be remote.
Cloud manufacturing is enabling smooth, secure, and agile operations during COVID-19.
The on-premise/off-premise line has previously been drawn utilising enterprise resource planning (ERP) software. But with new generation, fast, serverless solutions – along with improvements in bandwidth and the upcoming 5G revolution – we'll see more and more traditional shop-floor capabilities move to hybrid or full cloud architectures.
COVID-19 has accelerated the adoption of cloud manufacturing, and enterprises caught without enabling technologies will struggle to pivot as successfully as those who are future-ready in their manufacturing operations.
How can we help if you need remote access solutions?
Need to move to remote access for operational data management due to lockdown?
TilliT can help.
We are offering a free access option to our software for Production Scheduling and Digital Operations and a no-obligation 1-month trial.
With our assistance, you can transform your existing operations to our cloud system and receive up to five hours of onboarding support, on us.
If this sounds like an option worth discussing, or you want to improve your manufacturing operations in other ways – such as equipment and shop floor monitoring – contact TilliT.
Ask us how we can install IIoT sensors and configure monitoring solutions in less than one day.
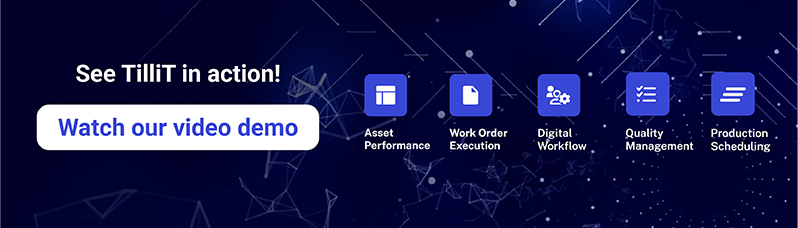